The manager of a furniture factory finds that it costs a significant amount of money to produce furniture. This is due to the high cost of raw materials, labor, and overhead expenses. The manager must carefully consider all of these costs in order to set prices for furniture that are both profitable and competitive.
In addition to the direct costs of production, the manager must also consider the indirect costs, such as marketing and administration. These costs can also have a significant impact on the overall cost of furniture.
The Costs of Production: The Manager Of A Furniture Factory Finds That It Costs
Furniture production involves direct costs such as raw materials, labor, and overhead expenses. Raw materials include wood, fabric, and hardware. Labor costs cover wages and benefits for workers involved in production, while overhead expenses include rent, utilities, and insurance. Furniture production also incurs fixed and variable costs.
Fixed costs remain constant regardless of production volume, such as rent and depreciation. Variable costs, like raw materials and labor, fluctuate with production levels. Economies of scale play a role in furniture production costs, where larger production volumes often lead to lower per-unit costs due to efficiency gains and reduced overhead expenses.
Factors Affecting Costs, The manager of a furniture factory finds that it costs
Furniture production costs are influenced by several factors, including the type of wood used. Higher-quality woods, such as mahogany or oak, typically command a higher cost. The complexity of the design also affects costs, with intricate designs requiring more labor and materials.
The efficiency of the manufacturing process is another factor, as optimized processes can reduce waste and labor requirements. Additionally, the relationship between quality and cost is crucial, as higher-quality furniture often requires premium materials and skilled craftsmanship, resulting in increased costs.
Technology can be leveraged to reduce costs through automation and improved efficiency in design, production, and inventory management.
Cost Control Measures
Furniture factories implement various cost control measures to optimize production efficiency and minimize expenses. Inventory management is critical, ensuring optimal stock levels to avoid overstocking or stockouts. Lean manufacturing principles focus on waste reduction, process optimization, and continuous improvement, leading to significant cost savings.
Other cost control measures include negotiating favorable terms with suppliers, optimizing production schedules to minimize downtime, and implementing employee training programs to enhance productivity.
Pricing Strategies
Furniture pricing strategies vary based on factors such as target market, competition, and product differentiation. Common pricing strategies include cost-plus pricing, value pricing, and competitive pricing. Cost-plus pricing sets prices based on production costs plus a profit margin. Value pricing focuses on delivering perceived value to customers, justifying higher prices based on unique features or benefits.
Competitive pricing aligns prices with competitors, considering market conditions and competitive offerings.
Financial Management
Financial management is essential for furniture factories to ensure financial stability and profitability. Key financial statements include the income statement, balance sheet, and cash flow statement. Financial ratios, such as gross profit margin, inventory turnover, and debt-to-equity ratio, provide insights into a factory’s financial health and performance.
Effective financial management enables informed decision-making, risk management, and long-term sustainability.
FAQ Corner
What are the major costs involved in furniture production?
The major costs involved in furniture production include raw materials, labor, and overhead expenses.
How can the manager of a furniture factory reduce costs?
The manager of a furniture factory can reduce costs by implementing cost control measures, such as inventory management and lean manufacturing principles.
What are the different pricing strategies that can be used for furniture?
The different pricing strategies that can be used for furniture include cost-plus pricing, value pricing, and competitive pricing.
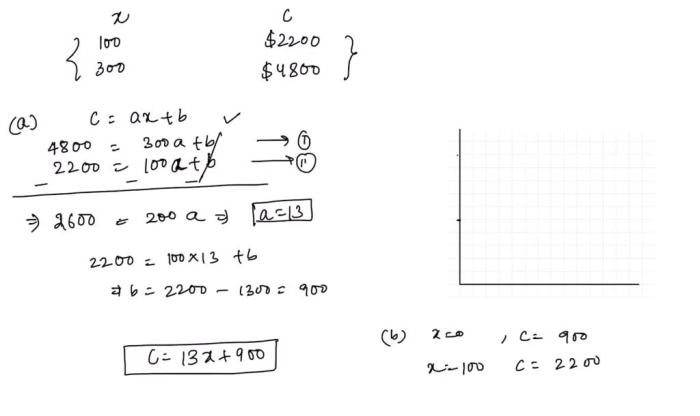
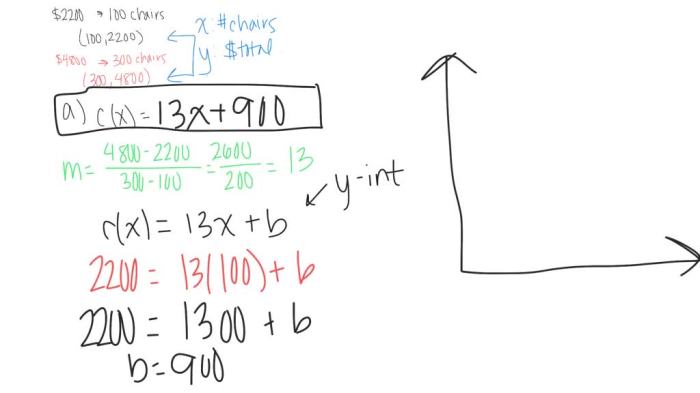